The charcoal machine production line processes raw materials such as raw wood, bamboo, and biomass briquettes into charcoal through steps including crushing, drying, briquetting, and carbonization. Mechanized charcoal has gained global popularity due to its high hardness, long burning time, and pollution-free characteristics.
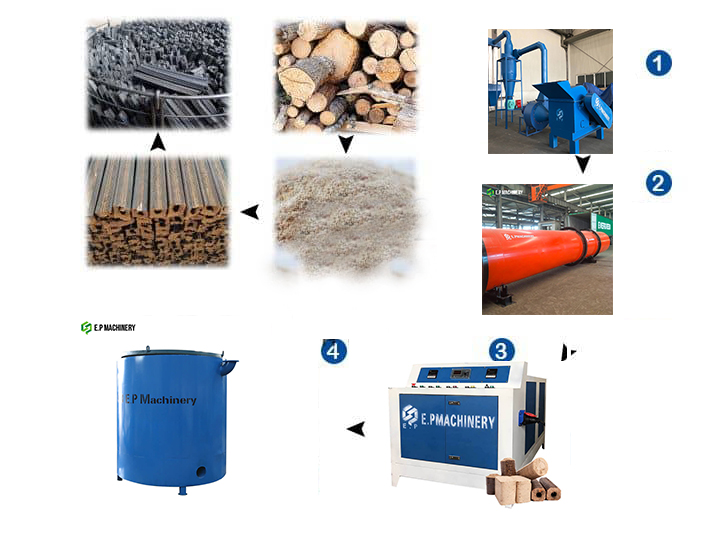
Production Line Workflow
The charcoal production line features a straightforward process: Crushing → Drying → Briquetting → Carbonization. Conveyors connect each step, allowing efficient operation with minimal labor—only 3-5 workers are needed for production.
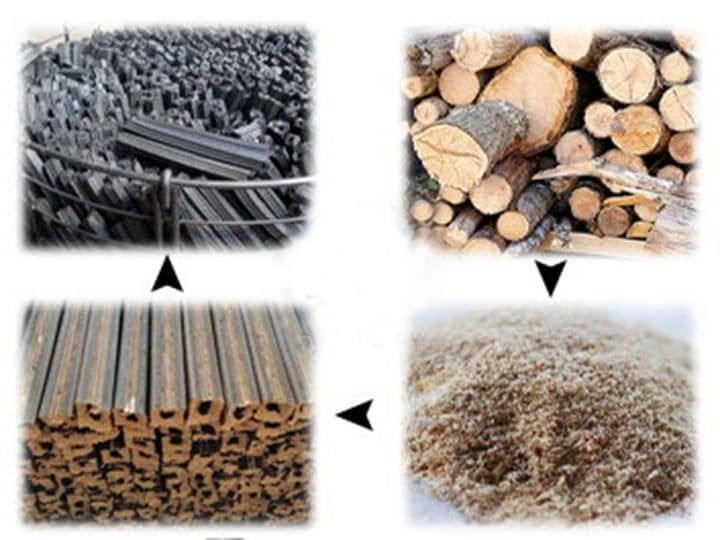
Structure of the Charcoal Production Line
Key equipment includes a wood shredder, sawdust dryer, biomass briquette machine, and carbonization furnace. These form the core of mechanized charcoal production.
1. Wood Shredder (Crushing)
The shredder breaks down raw materials (branches, wood scraps, bamboo, etc.) into 3-5mm wood chips, ensuring optimal particle size for charcoal formation.
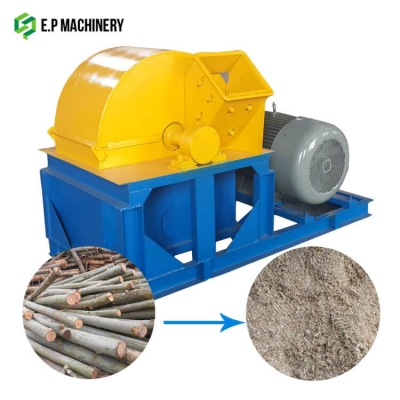
2. Sawdust Dryer (Drying)
The dryer reduces moisture content in wood chips to around 10%, a critical step to guarantee charcoal quality.
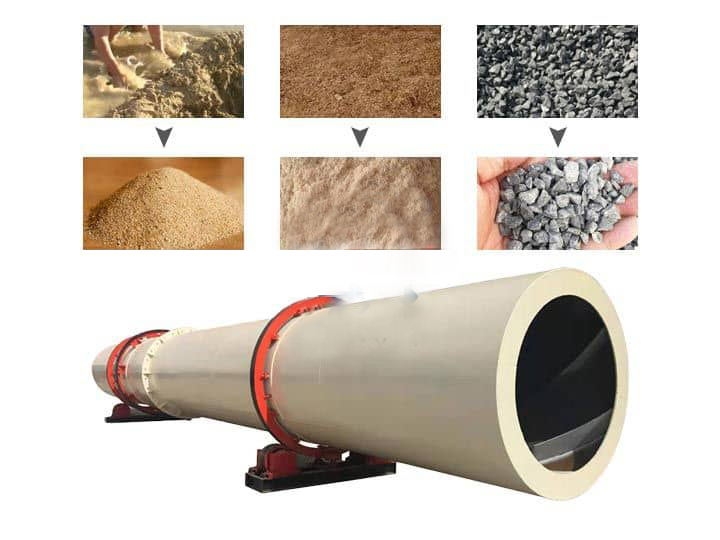
3. Biomass Briquette Machine (Forming Raw Charcoal Rods)
This machine compresses dried wood chips into hollow charcoal rods. As a core component, its proper calibration directly impacts product quality.
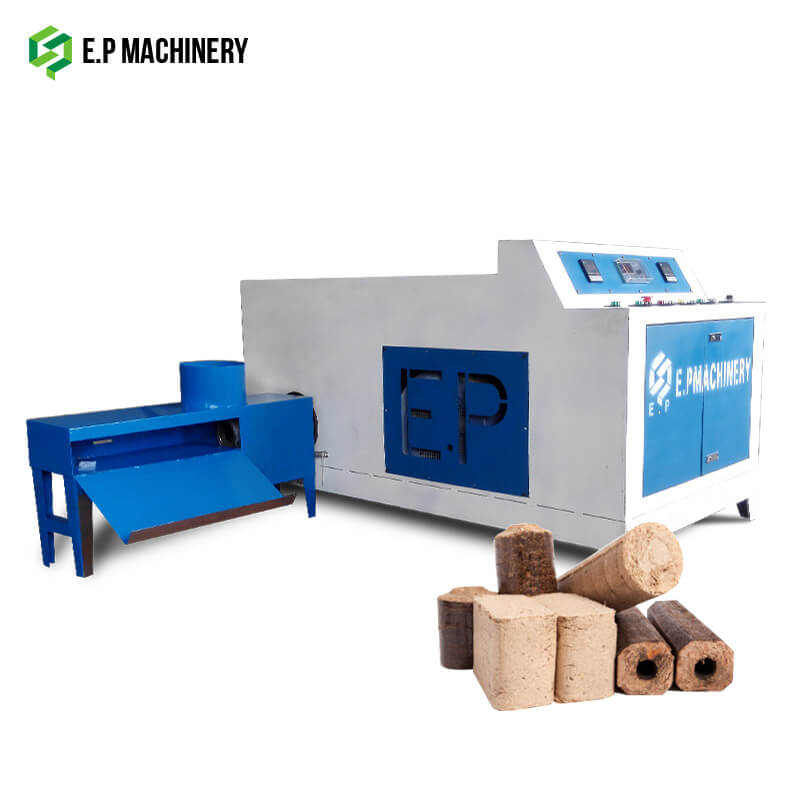
Features of Biomass Charcoal Rods
Compared to coal, branches, or straw, biomass charcoal rods produced by this line offer higher yields, greater demand, and broader acceptance. Key advantages include:
- Superior Quality: High marketability and profitability.
- Eco-Friendly: Pollution-free combustion.
- High Efficiency: High calorific value (long burning time).
- Aesthetic Appeal: Uniform and visually appealing shapes.
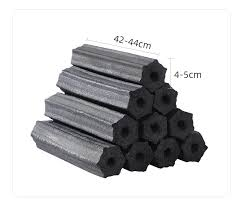